My travel collectible is hats- generally everyday ballcap style hats that I wear daily- bonus points for unique features/materials but generally practical, neat hats from around the world/country. I have a majority of US states, and a long list of countries represented, but most- particularly the caps also include a titled location. This detail often sparks fun conversations and kind of cements the trip/experience. However, once in a while I end up with an unlabled fancy hat- and this was the case during a quite memorable trip to the Shakori music fesival this past year. My lovely wife bought me this high end “Indiana Jones” style handmade leather (I’d not buy this for myself- it is now officially my most expensive hat). Conspicuously lacking an ID and particuarly in need of one given the “Shakori experience” I started mulling over how to confidently create a branded “SHAKORI” stamp to apply that captures the spirit of Shakori. (Also, I was eager to test a theory I had that it should be possible to cast metal using a Tig torch).
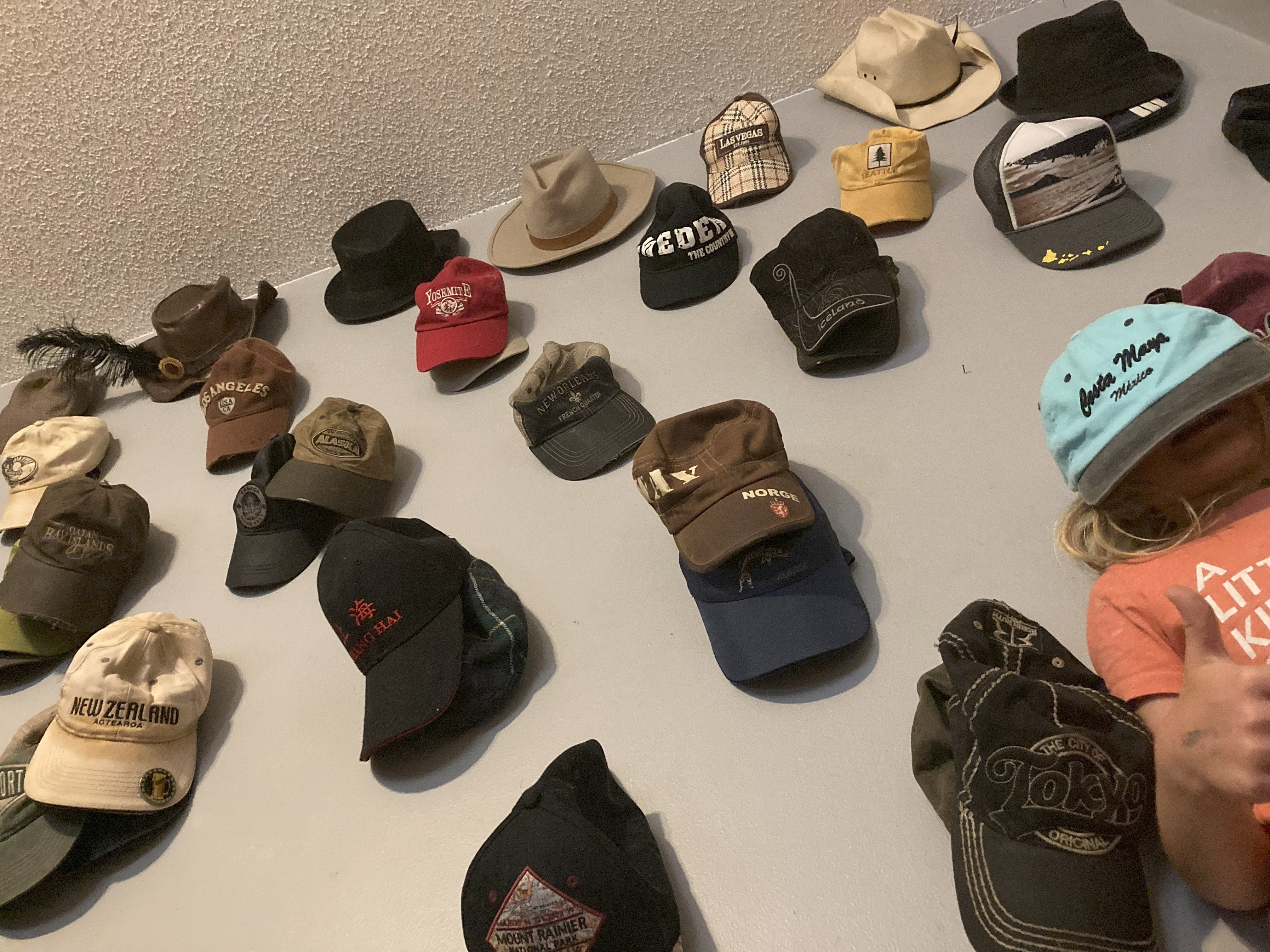
Here’s what I ended up with:
Step 1: Print a pattern. If you have a resin printer- thats probably going to be your best choice. I have 2 filament printers, and one resin. A little known trick in the filament printer slicer is that you can import a 2d image (preferrably monotone in this application) and the slicer will convert it into a 3d mesh model. It’s a simple feature that doesn’t allow you to add things you might like like draft or really any other details, but it actually does a great job with the conversion task. This is something you’d expect a high end CAD software like Solidworks or whatever to have, but even though there are features to attempt this, it turns out they’re generally embarassingly bad in my experience. So, you can also export as an STL file which is great- you still have a mesh file and not a solid model but for this purpose it works.
So after exporting my STL file, I can import it into my resin printer slicer no problem (the resin slicer lacks this feature) and print away. (Of course this would also work with a filament printer) This makes for a great high-resolution pattern, I just had to bond it to a plastic base for some extra molding space for material. I also drilled & tapped a few screw holes to act as release pins- that part is tricky since there is no draft and the overall mold is rigid you will want to pull out the pattern VERY gently and very straight. A good way to do that is to twist some small screws into the hardened plaster mold evenly until your pattern pulls free from your plaster mold.
Step 2:
We made our mold from garden variety Plaster of Paris with some manually chopped up fiberglass to give it some structure. It took a few tries to get it right (not shown) and the try that eventually “worked” I mixed thicker than I should have and so we had to machine a few bubbles that we couldn’t quite knock out. After the 1st attempt at “steam casting” didn’t quite deliver, we took it to the next level by adding a little vacuum block attached to a stainless tube. We dried out our mold firstly by just leaving it in front of a portable space heater for a few hours and then leaving it in a toaster oven overnight at around 350F. In the last hour or two we cranked that oven to max (500F’ish). Also, I sprayed on some of the high temp BBQ paint to the outside of the plaster mold in the hopes that it would help seal the exterior and therby direct the vacuum more directly toward the target area.
With the dried, pre-heated plaster+fiber mold heated & sealed we were ready to pour. I cut a groove in a kiln brick and melted down a pile of aluminum from a cast electric motor chassis. The meltdown produced a lot of slag but it was easy to pour the consolidated result into a nice clean ingot. I had read that engine pistons are a nice source of aluminum alloy with good casting properties but I took that to mean anything that was made from cast aluminum would be a good source. So far so good.
I used my largest Tig electrode (1/8?) and it actually made pretty short work of things once I got the settings right. I could keep reheating the pool of aluminum and used a 6061 aluminum extrusion to maintain the arc. When it was red hot and juicy I poured it in.
As soon as I removed the mold from the oven, I clamped the tubing into a vice and D attached a silicone tube to the stainless one which was already running the vacuum pump. After pouring in the aluminum, I attempted and promptly screwed up the “steam casting” part of the plan when the wet paper towel fell out of my bent tuna can. Still- there was a bit of steam and a nice impression of a tuna can on the bottom… so maybe it did something? I dunno.
Anyway, I used this mold despite some observed bubbles in the hopes that I could still end up with a flat text plane and sure enough some extra filled spaces appeared. I did cheat a bit and machine a few of those out but its also true that they were resolved enough sufaces that you could generally cut/pry out those defects with an X-acto. If I tried this again (I’ll need a new excuse) I think I could render an entirely clear result. As is, the end stamp does what its supposed to and it looks about as good as it could, so this was a fun experiment with a happy ending. It took longer than I expected and the video highlights the success part… still, I’m going to just let it be long- feel free to skip to the fun parts if you’re in a hurry.