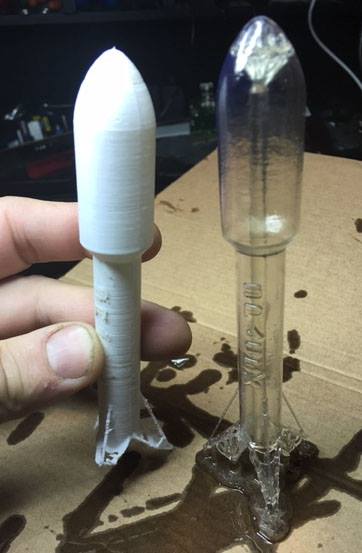
It occurred to me recently- & to my surprise that lots of people still aren’t clear about just what 3d printing is and what it’s good for. The short answer is: Lots! But not everything! Also, the term “3d Printing!” is an umbrella term covering all sorts of processes/materials & costs. So I’m going to try to do a quick summary to help clear things up:
3d Printing has been around since the late 80’s, but its only in the last decade that its become popular and pop’ed onto the radar of the general population. Some of the original machines bonded paper sheets together, or used melted wax. Chuck Hull/3D-systems is widely considered the first company to produce a practical 3d printer for industrial use- and their machine worked using SLA technology (photo sensitive resin). Refined versions of this approach remains valid and popular even today.
“Additive manufacturing”- a synonymous term describes any method of prototyping in which you add materials to create a part (typically a prototype, but in recent years some production things are made this way). There are 3 main categories popular for this and they are as follows:
FDM– “Fused Deposition Modeling.” (also FFF and others, but I hate that people keep changing up this acronym for no great reason, so I’m sticking with this classic). When somebody says they have a 3d printer, it’s probably this type, and for great reasons:
1. It’s cheap- like crazy cheap. These machines used to cost six figures and be the size of a closet. Now you can probably get them for under $100 if you try hard enough. These machines use stepper motors to move either a head, a build plate, or both around and melt the filament (typically PLA- a versatile plastic available in any color with a low melting point) one layer at a time to build a part along with any needed support structure. The plastic is pushed through a hot nozzle and squishes out like a (tiny) tube of toothpaste. You can build one layer on top of the next, but since the material would just fall to the ground if the overhang is too great, additional material is added strategically by the program when needed and is meant to breakaway after the print is removed. Some machines can be setup with two heads and in that case you can use a different material such as support that dissolves in assorted chemicals for especially detailed or delicate builds but for most parts everything is the same material- some parts can be built with no support structure at all.
2. You can use a wide variety of materials. PLA is the material of choice because it has a very low melting point, good surface finish, is cheap, has good bed adhesion, low distortion, and there is a broad array of colors, textures, and composites available. In short, many materials require a tricky balance of variables to optimize results (fan speed, enclosure, adhesion promoter, self-leveling probes…etc etc.). PLA just behaves the best and if you’re just having fun printing gadets is probably what you should buy. Some printers can be damaged trying to print other materials without required upgrades. BUT if you’re willing to make some adjustments and practice, it’s not too much of a stretch to get printing materials like PETG, Nylon, Polycarbonate, TPU (flexible, stretchy filament). No other process is more versatile than FDM.
3. Convenience: Compared to other methods, once you have your files, you just send and walk away. A few hours later you pop off a part and you’re ready for more! I’m starting to sound like an FDM salesman here, but really this is a tough to beat set of advantages. I have two FDM machines here- one modified single head machine (for now) with a 500mm cube capacity. It’s kinda slow but does a really good job, even on giant parts- I built a cabinet for it to normalize temperature, and added a laser diode so it can do some light duty engraving/cutting when not in use as a printer. My other printer is a dual head smaller machine but still enclosed. I think this smaller size allows it to deliver better results, and the dual head is nice for specialized prints. All of these are (now) direct drive rather than bowden which means a heavier (typically slower) head but better control especially over flexible filaments.
4. Scale: The simple design of these machines allows them to scale up without too much fuss. Consequently you can build really big parts by just stretching the gantry parts of the machine. Your build time will be proportionally scaled, but other technologies cited here all have more constrained size limitations. Last I saw companies were printing functional boats and full scale movie scenes with giant house-sized printers. Neat!
One of the only drawbacks to FDM is that at some level you can generally see “stairstep” patterns over the printed surface. While this is true of nearly every process, FDM particularly has a limitation when you want to reduce this effect by making shorter layers, it reduces your overall part strength and requires more pressure to push out material- there is a practical limit to torque that the steppers/gripping wheels can apply which translates to the required pressure that you’d have to generate to print super thin layers. So not only to do you start to lose strength, but time to print starts to skyrocket pretty quickly. In fact if you want the strongest/fastest parts you’ll want to print big, thick layers- which will exacerbate the stair-step texture. If you’re going to paint your parts anyway, its usually not too big a deal to finish out that texture with some practice and effort, so this surely isn’t a deal breaker.
SLA– “Stereolithography” is another popular printing technology generally these machines are common among more experienced users who need higher levels of detail or transparency. “SLA” is also another classic term for “Stereo Lithography”. The original machines built parts on a platform which descended into a photo-reactive fluid. It would take a lot of fluid to fill this vat and each layer was built on the surface of the fluid with the previous layer just under the surface. I think this helped with reduction/elimination of support structure as the viscosity of the fluid would allow it to support the part in a “weightless” state during the build. More recent versions of this concept invert the part and dunk the platform into a much smaller vat and use a release layer- (think transparent teflon) to build upside down, in a conceptually very similar way, but with a much more practical sized vat of expensive photo resin(fluid). This approach can deliver extremely high detail, and clarity for rigid parts. Some of these machines use a projector to flash a layer all at once, others (like mine) use a pair of galvanometers- basically servo operated mirrors to direct a laser. Resins are typically rigid and somewhat brittle, but these have been continuously improving. To be honest, I’m not certain what the state of the art resin is at the moment but even my SLA printer still surprises me at the results and it’s probably 6yrs old already. This is a great tool to use for patterns that get used to mold in silicone rubber, or plaster, or jewelry, dentistry… there are lots of very useful applications for this, but a reduced variety of materials compared to FDM. Most materials are going to look great but still be more breakable. You can also get generally transparent parts from an SLA and it polishes pretty well. That’s extremely difficult in FDM directly (owing to micro air-pockets typically trapped between layers)- though you can finish, mold, and cast clear parts if you wanted to get there the hard way.
SLS– “Selective Laser Sintering” This is actually one of my favorite methods to make parts, but unless they’re in the industry, almost nobody at your local makerspace will have one of these at home. The name actually describes it pretty accurately- this method involves a large bed of precisely smoothed powdered material. Like the previous methods, software evaluates your part(s), slices them into sections and then builds one layer upon the next. The difference here is that since parts are built from this powder, the powder IS the support structure, so you can build wild shapes in about any orientation and they will still get accurately formed. A laser traces these layers into the powder to sinter it together into a solid. At the conclusion you can dump or blow out the powdered material and have a nice, strong, solid, watertight, accurate part from nearly 100% pure material. Nylon is a popular material for this but there is some good variety in this area as well. “DMLS” is pretty much the same thing but with powdered metals and a lot more expensive. Really any of these machines will generally cost 6 figures, although some attempts have been made to scale these down to home or office use, you can count on these still being fairly high maintenance, large, and perhaps a bit messy so I’d be (pleasantly!) surprised to see these scaled down to offer much competition to the benefits I can get from my machines. In the case that I do need SLS or DMLS parts, there are lots of vendors to choose from. Fun fact: An awesome use of DMLS technolgy is in aerospace- companies like SpaceX are consolidating assemblies into simplified “superparts” and implementing them directly into actual rockets. This is a great and exciting example of using this technology to build cutting edge parts that simply cannot be manufactured any other way. It also opens up new opportunities to innovate in ways that never existed prior.
I’m always happy to talk about 3d printing in more detail- there’s a lot more to it of course. In nearly all cases, its a great tool for the work (& play!) I do- it’s great for relatively quick parts to test, evaluate, and redesign. It’s generally not a great choice for production of things. A great use, however is custom manufacturing- because each part can include specific features present in no other part. Want to print a million different snowflakes? No problem. Try that with conventional injection molding!